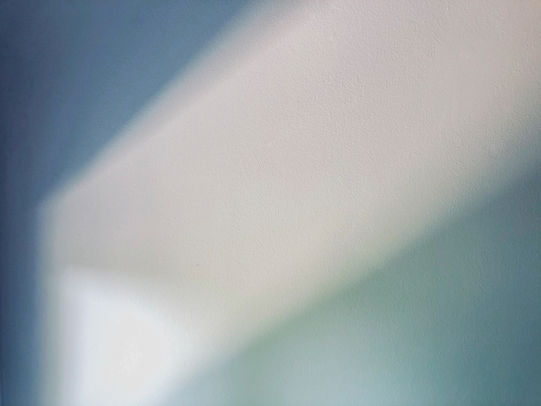
Caribbean Rum Distillery
The aim of this project was to build a new rum distillery in the Caribbean. Based on the success of a previous project with the client, FDT were appointed to lead the process design and project management of the project up to the point of installation and commissioning of the new distillery.
The distillery takes in fresh sugar cane juice from an integrated milling facility. The cane all comes from the island. The fresh made rum is put into casks on site and then matured.
The Aims
Rum distillery utilities assessment was focused on 3 main areas:
1. Biomass Boiler -
-
Bagasse fueled boiler
-
Pre-heating air is used to dry the bagasse while traveling along the vibrating grate prior to entering the boiler.
-
Boiler needs to operate at >30 bar(g) in order to have a high enough furnace temperature
-
Bagasse's density and calorific value is low and dependent of cane varietal and performance of the mills
-
An economiser is designed to withstand full boiler pressure thus pre-heating feedwater in excess of 100°C, this is important for efficiency
-
Turndown ratio 1:8 – all equipment on VSDs (min. turndown on feedwater pumps limited by pressure requirement i.e. 30 bar(g)
2. Organic Rankine Cycle Turbine -
-
ORC turbine is used as a steam load management device, otherwise, when there is no distillation taking place the steam would have to be vented.
-
Cycle based on Rankine’s steam cycle expect organic refrigerants/alcohols are used in the circuit in lieu of steam
-
Typically needs a heat supply and connection to cooling plant in this case steam supply of main header and cooling tower water connection
-
The circulating pump on the refrigerant circuit is VSD controlled giving a good turn-down ratio (albeit at lower output the parasitic loads consume a larger portion of the useful energy produced)
3. Air Emissions Abatement -
-
Feedwater economiser and air pre-heater
-
Grit collector or multi-cyclone separator operates with a pressure drop > 2 kPA
-
Reverse jet back filter – fitted with differential pressure instruments
-
> 95% particulate reduction achievable
The Solution
As part of the project the following activities were completed by FDT.
-
Feed in to initial site suitability assessment.
-
Process design, including cane handling (liaising with specialised suppliers), rum distillation and vinasse handling.
-
Full site utility design, including power generation.
-
The supervision and coordination between the different process vendors involved with the project.
-
FDT supervised and co-ordinated the installation and commissioning of the distillery in the summer of 2019.





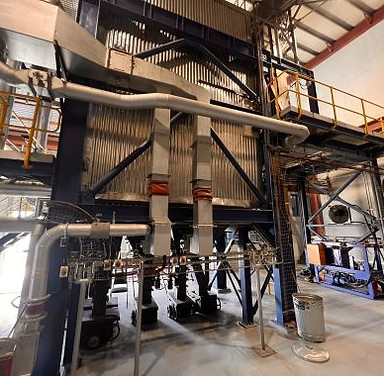